Magnetic refrigeration
Almost a century of demagnetization cooling
Magnetic refrigeration is a well-established technique that was proposed and first implemented back in the 1930s. It can be used to generate sub-kelvin temperatures by exploiting the magnetic field dependence of the entropy of a spin system. This is illustrated in the graph, which shows the entropy as a function of temperature for an ideal spin ½ system.
At high temperatures, the spins are randomly oriented, and their entropy is constant. In contrast, at low temperatures, the entropy of the spin system is a function of the magnetic field B and the temperature T. In this regime, reducing the magnetic field from point (B) to point (C) under adiabatic conditions – i.e., while keeping the entropy constant– will result in a decrease of the temperature. For this reason, magnetic cooling is also known as ‘adiabatic demagnetization refrigeration,’ or ADR for short.
For a more accessible explanation of how magnetic refrigeration works, you can check out this blog post, where we break down the key concepts in simpler terms.
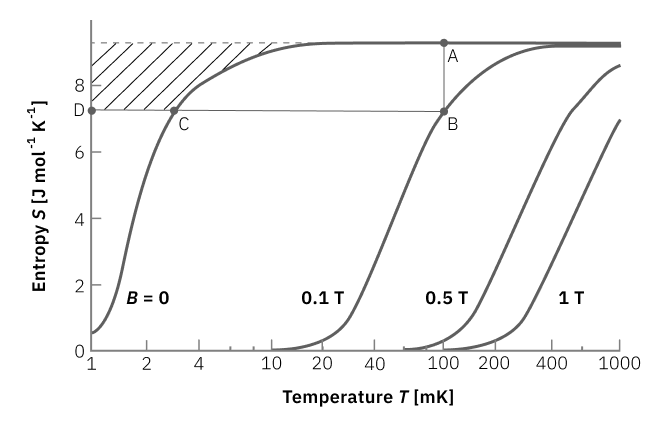
ADR – Adiabatic Demagnetization Refrigeration
How magnetic cooling works
A typical ADR configuration consists of a pre-cooling unit, typically a closed-cycle cryocooler, a heat switch, a superconducting magnet surrounding a solid-state cooling medium and a sample platform.
At the beginning of the ADR process, the heat switch connecting the ADR with the pre-cooling unit is closed and both the cooling medium and the attached sample stage are cooled to the cryocooler base temperature of about 4 K.
While the heat switch is still closed, the cooling medium is magnetized by driving a current into the superconducting coil. The heat of magnetization is released and dissipated in the main thermal bath provided by the cryocooler.
Therefore, after the maximum magnetic field has been reached, the cooling medium will return to its base temperature. The entropy of the system is now essentially determined by the magnetic contribution of the spin sub-system of the cooling medium.
Then the heat switch is opened to break the thermal connection between the pre-cooling unit and the cooling medium. By reducing the magnetic field adiabatically, the temperature of the cooling medium drops thereby cooling the attached sample stage.
Then the heat switch is opened to break the thermal connection between the pre-cooling unit and the cooling medium. By reducing the magnetic field adiabatically, the temperature of the cooling medium drops thereby cooling the attached sample stage.
Once the magnetic field has been reduced to zero, the ADR process can be repeated. The time to regenerate, i.e. to re-magnetize and relax the cooling medium, will usually be 1-2 hours, resulting in typical duty cycles of 70 to 95%.
cADR – continuous Adiabatic Demagnetization Refrigeration
How to provide long-lasting sub-Kelvin temperatures without cryogens
To provide continuous cooling without cryogens, we consider a system with two ADR units, where, similar to the conventional ‘one-shot’ ADR configuration, the first unit is connected to the main thermal bath via a heat switch. But this time a second ADR unit is added. It is connected on one end to the first ADR unit using another heat switch and on the other end to the sample stage.
As shown schematically, the two interconnected ADR units will work together to extract heat from the sample stage and to pump it into the 4 K main thermal bath.
Besides this serial two-stage configuration, many different cADR layouts with multiple ADR units can be realized, including serial or parallel configurations and even combinations thereof.
The optimal configuration depends on the demands of the experimentalist and the specific experimental conditions.
Both the first and the second ADR unit are fully magnetized and connected through their respective heat switches. Therefore, the cooling media and sample stage initially have the temperature provided by the cryocooler.
Unit 2 is decoupled from unit 1 and demagnetized, thereby cooling the sample stage down to the target temperature.
Unit 1 is disconnected from the bath and demagnetized, too. It stabilizes a temperature well below the setpoint temperature of unit 2. Now the heat switch between the two ADR units is closed and unit 2 can be regenerated, while at the same time the temperature of the sample stage is kept constant.
After unit 1 is depleted, the connection between the two units is opened again by opening the corresponding heat switch and unit 1 is regenerated at the temperature of the cryocooler.
This procedure can be repeated infinitely to provide continuous cooling at the sample stage.
Automatic operation
Turnkey cryostats
We believe that innovation and user-friendly design should be an essential part of cryogenics. We are devoted to manufacturing highly automated cryostat systems that can be operated without expert knowledge. Because they don’t require liquid cooling media in the cooling process, our cryostats are very robust and fully automatic.
All systems can be controlled using a modern, user-friendly graphical software that can easily be adapted to your preferred measurement equipment and setups.
Automatic Sample Changer
Our L-Type Rapid cryostats come with an automatic sample changer, featuring a top-loading load-lock mechanism for quick sample installation. Multiple users can prepare their experiments simultaneously using different sample pucks, which is useful for complex preparations that would cause significant downtime with conventional systems.
The sample loading process is also extremely fast: it takes seconds to plug a sample puck into the transfer cage and secure it inside the vacuum lock.
It then takes a couple of minutes to automatically load the puck to the low temperature stage, where it is cooled to the base temperature in less than three hours.
The whole process requires no manual work at the cryostat and avoids the need for fragile probe sticks, making it an ideal solution for less experienced users, shared facilities and industrial environments.
R&D projects
We actively shape the future of quantum technologies with R&D projects that encompass the development and deployment of integrated cryo-operating platforms for the quantum computers, quantum repeaters and quantum sensors of the future. We can therefore cover the full spectrum of groundbreaking quantum technology with our products and services – from superconducting circuits, ion traps and atoms for quantum computing, to NV centers and single photon detectors for sensing and communications applications.
CRYOFAST
CRYOFAST will make it simpler and more convenient for researchers and developers to access the very low temperatures needed for the development of quantum technologies.
LEMON
The focus of the LEMON project is to develop a scalable, helium-3-free cryogenic cooling solution capable of reaching milli-Kelvin temperatures.
MILLENION QUANTUM
kiutra is providing the cooling platform for the MILLENION project, a collaboration of 14 academic and industrial partners across Europe to advance trapped-ion quantum computers.
MUNIQC-SC
We are part of the MUNIQC-SC consortium, an initiative to build a quantum computer demonstrator based on superconducting circuits.
SPROUT
The goal of this project, launched in 2021 in partnership with Delft Circuits, was to provide a fully integrated, turnkey cooling platform as the go-to solution for quick and reliable testing of components or building multi-node quantum networks.
MATQu
We are part of the Materials for Quantum Computing (MATQu) consortium, which was set up to establish a European value chain for superconducting qubits.
EIC Accelerator Pilot
Supported by the prestigious EIC Accelerator programme kiutra is developing a unique characterization tool for qubits and related low-temperature electronics.
MARQUAND
The MARQUAND project was a joint effort of the Walter-Schottky Institute and kiutra. Its goal was to develop and operate highly efficient quantum detectors.
Glossary
Heat switch
A heat switch is a tunable thermal link. Heat switches are widely used in cryogenics and are a key component for every magnetic refrigerator.
In a magnetic refrigerator, a heat switch is used to decouple the ADR cooling medium from its pre-cooling stage during the demagnetization cooling. The heat switch is closed to conduct the heat of magnetization, which is generated during the regeneration process, into the pre-cooling stage.
There are several types of heat switches, each with different advantages and disadvantages. The most common types are mechanical switches, gas-activated heat switches and superconducting heat switches. Another distinction is between active and passive heat switches. With active heat switches, the switching process can be controlled by the operator. With passive heat switches, the switching process always happens at a certain pre-defined temperature.
Hold time
With a ‘one-shot’ ADR cryostat, the cooling medium can provide cooling only for a limited amount of time, the ‘hold time’, which is determined by the cooling capacity of the medium.
After the cooling medium is magnetized and the heat of magnetization has been dissipated in the pre-cooling stage, the heat switch is opened, and the cooling medium is partially demagnetized. During demagnetization of the cooling medium its temperature drops. Once the target temperature has been reached, demagnetization of the cooling medium continues at a smaller field ramp rate, which is set to compensate for thermal leaks through the support structure, thermal radiation, or customer setups. The total time available at the target temperature is the ‘hold time’. It ends once the magnetic field has been reduced to zero, i.e., when cooling medium is fully demagnetized, and the cooling process terminates.
The hold time will vary as a function of temperature, so typically when the system is operated at the lowest temperature, the system may still be operated at higher temperatures by re-magnetizing the cooling medium.
A major benefit of magnetic temperature control is that temperatures can be stabilized with high precision, as no valves, capillaries, or heaters are involved.
One-shot
With a ‘one-shot’ ADR cryostat, the cooling medium provides cooling for a limited amount of time, known as the ‘hold time,’ which is determined by the cooling capacity of the medium.
After the cooling medium is magnetized and the heat from magnetization has dissipated in the pre-cooling stage, the heat switch is opened, and the cooling medium is partially demagnetized. During demagnetization, the temperature of the cooling medium drops. Once the target temperature is reached, demagnetization continues at a slower field ramp rate, which is set to compensate for thermal leaks through the support structure, thermal radiation, or customer setups. The total time available at the target temperature is called the ‘hold time.’ It ends when the magnetic field is reduced to zero, i.e., when the cooling medium is fully demagnetized, and the cooling process terminates.
The hold time will vary as a function of temperature, so typically when the system is operated at the lowest temperature, the system may still be operated at higher temperatures by re-magnetizing the cooling medium.
A major benefit of magnetic temperature control is that temperatures can be stabilized with high precision, as no valves, capillaries, or heaters are involved.
Stray fields
A common concern regarding magnetic refrigerators is the presence of magnetic stray fields at the sample position when the cryostat is running. We pay particular attention to these magnetic fields to enable measurements of very sensitive materials and devices.
In all our cryostats, we use compensated superconducting magnets to reduce the stray fields at the sample position and to minimize the magnetic interference between neighboring cooling units in multi-stage systems.
In our L-Type Rapid, we maximized the distance of the ADR magnets and the sample stage to minimize the stray field. Together with our compensated magnet coils this ensures stray fields of less than 50 µT at the sample position, which is similar to the earth’s magnetic field. As in any other cryostat, mu metal shielding can be used to further reduce these small residual fields. This makes the L-Type Rapid a suitable tool to probe sensitive materials and devices, such as superconductors or quantum electronics.
It is also noteworthy that the stray fields given in our specifications always refer to the maximum magnetic field in the cooling unit. In one-shot ADR cryostats, however, measurements are usually performed with the magnet operating at 0-30% of its maximum field, resulting in accordingly reduced stray fields. Similarly, in cADR systems, most of the magnets are operating at 10-30% of their maximum charge, which again leads to a reduction of the effective residual fields at the sample position.